Ну вот дошла очередь и до головы. Как и пологается, сначала полная разборка и дефектовка:
1. ГБЦ. Все мифы хозяина о доработанной голове развенчались, каналы стандартные, и ни чего с ними не делали, постели валов и посадочные гидриков в норме, привалочные плоскости ровные, голову помыл, мыл средством для очистки двигателя, бензом и растворителем, потом водой с последующей продувкой, мойка не окончательная, так как придётся ещё после расточки тщательно мыть.
2. Валы действительно злые, конечно производителя я так и не установил, хотя и стоят маркировки на торцах 98, но промер базы и высоты кулачка выдал результат 10,8 мм, оно и видно что произведена наплавка с дальнейшей проточкой под нужный профиль, шеи валов более менее, есть конечно небольшие царапки, но не криминал, люфт в постелях в допуске, единственный косяк на валах, это выработка от сальника, довольно большая, такое ощущение что они прошли не меньше 200 тыс км, а то и больше, но так как валы пока не планирую менять, проблему решу смещением сальника.

3. Гидрики видно потрёпаны жизнью, все в царапках, может они и рабочие, но испытывать судьбу не буду, поэтому под замену.
4. Пружины и тарелки остаются
5. Клапаны. Промер и внешнее состояние показали пригодность, но так как в планах резануть каналы, то они будут заменены на облегчённые.
6. Направляйки. Изначально думал заменить их на бронзовые, но потом решил, а где гарантия что под видом бронзы не пришлют латунь, доверия к интернет магазам пропадает с каждым новым заказом (об этом в следующих записях), поэтому решил промерить зазор клапан-втулка, отыскал несколько доступных способов, за неимением микро нутромеров:
Первый это так сказать звуковой и самый быстрый, вставляем клапан во втулку заподлицо с верхним краем последней, плотно затыкаем пальцем отверстие, и резко вытаскиваем клапан, если в момент выхода клапана из втулки слышится отчётливый "чпок", значит зазор в допуске.
Второй способ немного точнее, с помощью тонких листов бумаги, подобрал несколько листов от газет и журналов, толщину замерил микрометром, нарезал полоски шириной около 3мм и длиной около 10см, получились эталоны толщиной 0,06, 0,05, 0,04мм, и самая тонкая это копирка толщиной 0,03мм, переходим к замерам, вставляем полоску в втулку, потом туда клапан, не лезет, значит берём следующую полоску, лезет плотно значит зазор равен толщине полоски, лезет легко значит берём следующую полоску по толщине выше, и таким образом определяем зазор.
Отбраковал всё, и теперь уже надо готовится к более ответственной работе - шинковке каналов, так как бошка одна и тестовой у меня нет, а тем более в первый раз предстояла такой хренью заняться, то решил не спешить, а подготовиться как следует, а именно набраться информации и приготовить фрезы. Цены конечно на них кусь-кусь, и в наличии в магазах больших диаметров не найти, поэтому буду делать сам, единственно на что пришлось потратиться, это на шаровую фрезу 17мм, и то такая пиз.юлина пятихаточку стоит.
Занялся поиском заготовок для фрез, в ход пошли пальцы шаровой и рулевой классики, пальцы от рулевых тяг других авто, в общем всё что попадалось с пальцами всё вскрывалось, но одними пальцами не обойтись, поэтому взял справочник по шарикоподшипниками и выбрал несколько, в которых находились нужного мне диаметра шары, все они грузовые и если покупать для такого дела очень дорого, просто у меня была возможность раздербанить нульцевые и выковырять необходимое, а именно шары для прохода каналов от сёдел, с диаметрами около 22 и 26мм.
Разметил, к шарам приварил высокие гайки под резьбу М8 и М10, и начал резать зубы, чем больше зубцов тем аккуратнее будет грызть, поэтому делал максимально, на каждую фрезу уходило минут 15 времени, тут я конечно немного перегрелся и нахеракал фрез всевозможных, также сделал фрезы прямозубые из развёрток, так на всякий случай.



Надёжно закрепил голову на площадке болтами М6 через отверстия болтов гбц, м-ду бошкой и площадкой картон, чтоб не царапать плоскость, сама площадка это фанера прикрученная к брусу, всю эту систему зажал в тисы,
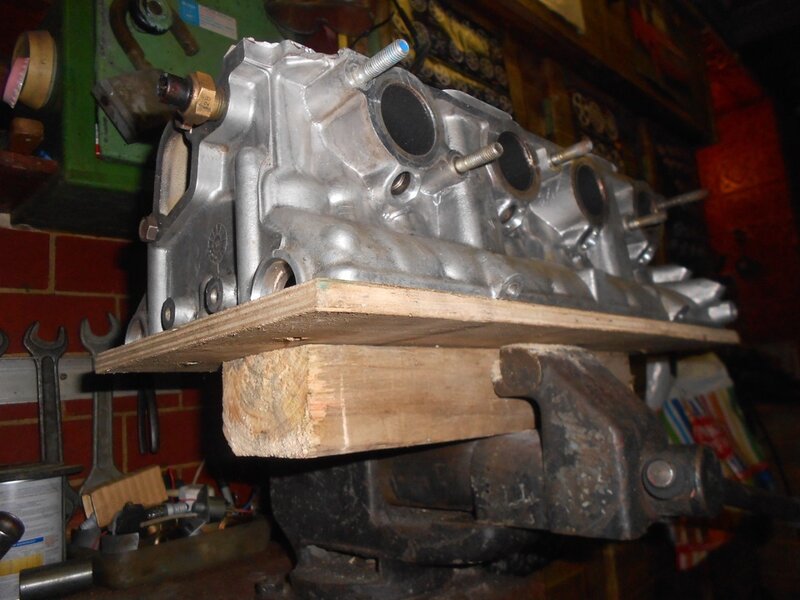
плоскость головки со стороны блока заклеил двумя слоями самоклеящейся плёнки, дабы по случаю не покарябать и как потом оказалось не зря.

И вот начался процесс расточки, сначала срезал выступающие части втулок, шаровой 17мм фрезой за 500р, это единственное для чего она пригодилась, ну а потом своими фрезами стал дорабатывать каналы, после фрез выровнял каналы наждачкой, для этого взял шпиль с прорезью,

начинал шлифовку с 40 наждачки, закончил впуск на 80, выпуск на 280 и затем полировка пастой ГОИ, весь процесс подробно не описываю он стандартный, в итоге что получилось впуск со стороны сёдел 26мм, со стороны рогов 37мм, выпуск сёдла 22мм, коллектор 33мм. Впуск будет с фаской на расширение канала у рогов, т.к рога реса диаметром 40мм, выпуск не стал подгонять по прокладке, оставил ступень, судя по отзывам она должна быть, чтоб уменьшить обратный заброс выхлопных газов.
Фото до расточки
Впуск

Выпуск

И после
Впуск


Выпуск

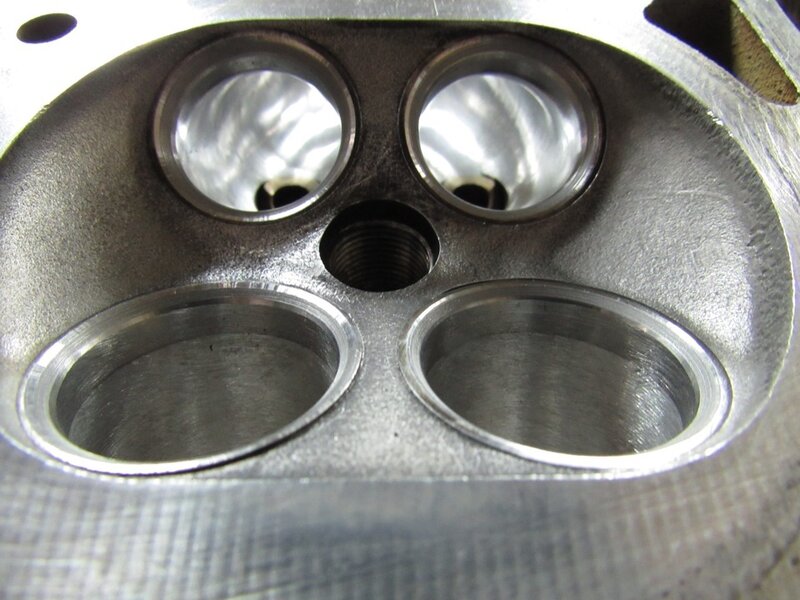
Общий вид



И вот работа сделана, процесс сдвинулся ещё на одну ступень, далее сборка ГБЦ.
Сообщение отредактировал САВЧА - 1.3.2015, 23:50